AMBA Parameter Configurable Multi-Channel DMA Controller (typically 1 to 256)
Guide to Choosing the Best LDO for Your Application
Originally Written By: Moises Robinson, Ph.D. and Jerry Rudiak
Revised: 2/15/2019 by Stephen M. Nolan
ABSTRACT
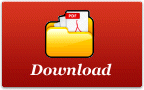
Low dropout voltage regulators (LDOs) are common in many applications. State of the art Power-Management Integrated Circuits (PMICs) for smartphones and other portable devices include over a dozen LDOs. LDOs are also found integrated onto Microprocessors, Graphics Processing Units (GPUs) and in many other Systems on a Chip (SOCs). To know which LDO you need, you must first define the application of your LDO and then examine which parameters are most important when dealing with that application. With the multiple parameters that characterize a particular LDO, it is not easy to determine which LDO is best suited.
To help you figure this out, we have put together this reference. This guide presents a list of all the key LDO parameters along with their definitions, the most common applications of LDOs, and which parameters are critical for each.
INTRODUCTION
Power management is an important design consideration for many products, especially for devices that rely on a battery for their power.
A voltage regulator is an electronic component that automatically provides a regulated and controlled output voltage to the various circuits inside an electronic device. The two main categories of voltage regulators are low dropout (LDO) linear voltage regulators and switching regulators. There is certainly a significant usage of switch-mode power supplies for the benefits they provide in power density and overall efficiency; however, LDOs are also used in a wide variety of applications today, and are an important component to understand and consider. For example, LDOs are used due to their low-noise output voltage, small size, low shutdown current and low cost when compared to switching regulators. The clean voltage they provide makes them an ideal choice for noise-sensitive, high-frequency; for example, Phase-locked loops (PLLs) for Microprocessors as well as for high-speed Serial links. With so many possible LDO applications and many parameters that can be optimized for each LDO, it’s not easy to determine which LDO is best suited for a particular application. There is usually a trade-off between achieving very low quiescent current (IQ) while also meeting other key parameters like excellent dynamic performance, low output noise, and high power-supply noise rejection. This whitepaper is intended as a tool to help system designers choose the best LDO for their application.
LDO FEATURES AND PARAMETERS
Different applications impose different requirements on LDOs. By clearly understanding the different LDO features and parameters and the requirements of their specific application, system designers can choose the proper LDO. Listed below are the important features and parameters and what they mean.
Capless Operation Feature
Most LDOs require an output capacitor for proper operation. LDOs that can provide their stated performance without an output capacitor are called “capless”. Capless LDOs are ideal for applications with challenging space requirements, such as smartphones and wearable devices.
DC Line Regulation Parameter
DC line regulation is defined as the resulting change in the output voltage for a given change in the input voltage. This measurement is made under conditions of low power dissipation.
DC Load Regulation Parameter
The DC load regulation is the change in output voltage for a static change in output (load) current.
Dropout Voltage Parameter
The dropout voltage is the differential voltage between the input and the output for which the regulator output no longer maintains regulation against further reductions in input voltage. Typically, the LDO dropout voltage is specified as the input voltage level that causes the output voltage to drop 100 mV below its programmed, regulated value. Since an LDO must provide the required constant voltage as the battery discharges, a small dropout voltage is very important as the smaller the dropout voltage, the greater the useful input voltage from the battery and therefore the longer the run time.
Efficiency Parameter
Power efficiency is defined as the percentage of the input power that is delivered to the output and it is expressed as:
In order to maximize the LDO efficiency, the output voltage to input voltage difference (VOUT/VIN), and the quiescent current (IQ) must be minimized.
Input Voltage (VIN) Range Parameter
The input voltage range determines the maximum and minimum allowable input supply for the LDO. Input supplies that are higher than the maximum allowable input can damage the LDO. The lowest input supply must be higher than the LDO output voltage plus the dropout voltage.
Maximum Output Current (IOUT) Parameter
This parameter is the maximum output current that the LDO can provide while meeting the datasheet parameters.
No Load Current Operation Feature
Several applications need the LDO to hold the output and provide good performance under a no-load current condition (e.g. CMOS RAM keep-alive applications). Some LDOs might suffer from degraded performance under no load conditions.
Output Noise Voltage Parameter
This parameter is the rms output noise voltage generated only by the LDO (including the voltage reference-noise as it is assumed that the LDO has an integrated reference) over a given frequency range (typically 10 Hz to 100 kHz) under a constant output current and a clean input voltage. Most of the noise comes from flicker noise in the internal LDO voltage reference.
Output Voltage (VOUT) Accuracy Parameter
The output voltage accuracy describes the typical and worst-case deviation of the output voltage with respect to the nominal LDO output voltage. The overall output voltage accuracy also includes the effects of line regulation and load regulation.
Output Voltage Range Parameter
The output voltage of an LDO may be fixed or programmable. If the output voltage is programmable, it is important to know the maximum and minimum limits of the output voltage programming range. The output voltage range specification provides this information. It is also useful to know the output voltage step size.
Over-Current Protection Feature
This feature limits the maximum amount of current that the LDO can source. This limit is established in order to protect the LDO and the system under an output shortcircuit or output high current condition.
Over-Temperature Protection Feature
This feature shuts down the LDO when the die temperature exceeds the specified high temperature level. The LDO is re-enabled when the temperature drops to a safe value.
Power Supply Rejection Ratio (PSRR) Parameter
The PSRR is a measure of how well the LDO rejects electrical noise at the power-supply input by measuring the change in output noise voltage.
Quiescent Current (IQ) Parameter
Quiescent current, also called ground current, is the current used to operate the LDO, and is not delivered to the load. It is measured when the LDO is enabled and the output/load current is zero (0). A small quiescent current is needed to maximize LDO output efficiency, reduce heat, and extend battery life in battery-operated applications.
Soft-Start Operation Feature
The soft-start feature guarantees that the output voltage will ramp-up slowly from zero to the required output voltage. Soft-start is useful to avoid inrush current during start-up operation.
Soft-Stop Operation Feature
Soft stop guarantees that the output voltage will rampdown slowly in a controlled fashion when the LDO is disabled.
Shutdown Current (ISD) Parameter
Shutdown current is leakage current through the LDO, when the LDO is disabled or powered down.
Start-Up or Turn-On Time Parameter
Start-up time is the time between the rising edge of the enable signal and the output voltage reaching 90% of its nominal value.
Line Transient Regulation Parameter
The line transient regulation parameter provides a measure of the ability of the LDO to maintain a constant output voltage with a transient step at the input.
Load Transient Regulation Parameter
The load transient regulation is defined as a change in the output voltage resulting from a given dynamic (step) change in the output current. Load transient regulation includes overshoot (difference between the maximum VOUT and the initial VOUT during a load transient regulation test when the output current changes to a lower value), as well as undershoot (difference between the minimum VOUT and the initial VOUT during a load transient regulation test when the output current changes to a larger value).
LDO SELECTION PROCEDURE
With so many key LDO features and parameters, it is usually difficult for system designers to select an appropriate or best LDO for a certain application. To make the LDO selection process easier, we recommend dividing the LDO parameters into three groups:
Basic DC Parameters
The LDO must operate within the range of required DC parameters to provide the required functionality for a particular application. A typical basic DC parameter is the input voltage range.
Required Features and AC Performance Parameters
The LDO must provide the required features and the parameters must meet the required AC parameters to provide the performance required for the particular application. A typical AC performance parameter is PSRR.
Optional Extra Features
These may or may not be required for a particular application. For example, if the LDO is part of a large SOC that already includes a temperature sensor, a temperature sensor inside the LDO may not be useful. Table 1 shows the features and parameters separated into each of these three groups. Efficiency is not included because it is a function of the input/output voltage ratio (VOUT/VIN) and the quiescent current (IQ).
Table 1. LDO Parameters Divided Into Three Groups
Basic DC Parameters | Features and Performance | Optional Extra Features |
Dropout voltage | Capless operation | Over-temperature protection |
Input voltage range | DC line regulation | Input voltage brownout protection |
Maximum output current | DC load regulation | Soft-stop operation |
Output voltage accuracy | No load current operation | |
Output voltage range | Output noise | |
Over-current protection | Power supply rejection ratio | |
Soft-start operation | Quiescent current | |
Shutdown current | ||
Start-up or turn on time | ||
Line transient regulation | ||
Load transient regulation |
To select the best LDO for your application, we recommend the following four-step process:
- Select a group of LDOs that meet the basic parameters for your application. For example, do you need a capless LDO for an embedded SOC application? What is the required dropout voltage? What input voltage range does the LDO need to support?
- From the group of LDOs chosen in Step #1, choose the LDOs that meet the parameters from the performance column of Table 1 that are important for your application.
- In this step, narrow your selection to the one performance parameter that is most important for your application.
- Now that you have made your LDO selection, find out which optional parameters the LDO IP Core offers for your application.
LDO APPLICATIONS
Listed below are a few LDO applications and the LDO performance parameters that are important for each. Please contact Vidatronic at sales@vidatronic.com if your particular application is not discussed in this white paper. We will gladly help you with your particular application.
Cameras (CMOS Image Sensor)
The analog supply voltage for most CMOS sensors used in cameras ranges from 2.4 V to 3.1 V. This voltage must be very clean for the sensor to support the camera specifications. Critical LDO parameters for this application are a high PSRR, typically at 100 kHz, and a low output noise.
AMOLED or LCD Displays
The embedded analog circuitry inside AMOLED or LCD Displays requires a supply between 2.2 V and 3.6 V provided by an LDO. The key LDO performance parameters required to enhance image quality are high PSRR, fast load transient regulation, and tight output voltage accuracy.
Digital IC Loads
LDOs are used to power multiple types of logic circuits including microprocessors, microcontrollers, embedded memories, and digital signal processor (DSP) blocks. The input voltage ranges for these digital blocks continue to be pushed lower (e.g. sub 1 Volt) and with tighter tolerances. To guarantee that the LDO output voltage always stays within the minimum and maximum levels, the LDO must have good output voltage accuracy, good line and load DC regulation, and fast line and load transient regulation with small overshoot/undershoot. The requirement for good DC line regulation directly translates into a requirement for good low frequency PSRR, since both parameters are a measure of how much the output voltage changes as a function of a change in the input voltage.
If the logic circuits are used inside handheld devices, low quiescent current (IQ) and low shutdown current (ISD) are important in order to minimize system power consumption in sleep mode. A fast start-up or turn-on time is also required when the digital blocks come out of sleep mode, and a small dropout voltage is highly desirable to power digital IC loads in order to optimize power efficiency.
Phase Locked Loops (PLLs) and Clock and Data Recovery Circuits
LDOs provide the clean power supply for most voltagecontrolled oscillators (VCOs) used inside Phase Locked Loops (PLLs) and Clock and Data Recovery (CDR) circuits. Such PLLs and CDRs are used to meet tight phase noise and clock jitter specifications in high-speed transceiver and serializer/de-serializers (SERDES) blocks. Critical LDO performance parameters for these applications include tight output accuracy, high PSRR, and low output noise.
High-Speed and High-Accuracy Data Converters
To get the optimum performance from high-speed or high-accuracy analog-to-digital (ADC) and digital-toanalog (DAC) converters, the data converter must be supplied with very clean DC power supplies and reference/bias voltages. Because noise on the supply can affect the converter noise level as well as the spurious performance of the converter, the power supply rejection ratio (PSRR) of the voltage regulator that generates the supply or reference voltages for the data converter is the most important parameter for data converter applications. PSRR in excess of -40dB for frequencies greater than or equal to 10 MHz may be required to avoid any high frequency noise degrading the data converter performance.
RF Sections in Portable Devices
The RF section in portable devices runs at higher voltages than the baseband functions and processor, reducing the difference between the input and output voltage for the LDO that powers the RF section. The current consumed by all the RF blocks is typically small (< 100 mA) except for the transmitter power amplifier. The low power and small difference between the input and output voltage make the RF sections of portable devices an ideal application for LDOs. Some critical blocks inside the RF section include input low noise amplifiers (LNAs), mixers, and PLLs. A clean power supply is required to meet tight RF receiver sensitivity and to avoid issues with transmit spectral purity, which are subject to government compliance standards. Critical LDO parameters for such applications include very low output noise, high PSRR at high noise frequencies, and fast start-up.
Audio CODECs
Portable devices must process several types of audio signals including voice and MP3 files. The audio CODECS in portable devices require clean power supplies in order to meet challenging resolution, Total Harmonic Distortion (THD), and dynamic range requirements of the Analog-to-Digital (ADC) and Digital-to-Analog (DAC) converters. Important LDO parameters for audio applications are tight output accuracy, high PSRR, and low output noise.
There are many other noise sensitive applications that require LDOs with low noise as well as high PSRR. These applications include test and measurements, medical equipment, base stations and communications equipment, among others.
VIDATRONIC HIGH PERFORMANCE LDOS
Vidatronic capless LDO Intellectual Property (IP) Cores offer unparalleled performance, which make them ideal for a host of power applications. Using our Noise Quencher® technology, our LDO IP Cores have several features that add significant value to the overall system solution:
- Smallest overall solution due to capless operation (no need for an output capacitor)
- Output voltage accuracy better than ±1%, without trimming
- Output current (IOUT) higher than 1 A
- Power supply rejection ratio (PSRR) better than -40dB up to 10 MHz
- Overshoot/undershoot less than ±50 mV without an output capacitor
- Unconditional stability regardless of output capacitance used, including capless
- Controlled soft-start and soft-stop operation
- Over-current and over-temperature protection
- Dropout voltages of less than 30 mV for 100 mA output current
- Small silicon area and reduced pin count through capless operation
SUMMARY
Low dropout linear voltage regulators (LDOs) are a key component used in multiple applications. With this simple procedure and parameter/application reference, system designers can select the best LDO for any application.
For more information on Vidatronic’s advancedarchitecture LDO voltage regulators, go to: http://www.vidatronic.com/ip-solutions/ or contact Vidatronic at sales@vidatronic.com to learn how we can provide the best LDO IP Core for your application.
Title
- Guide to Choosing the Best DC-DC Converter for Your Application (2016)
- Introduction to Low Dropout (LDO) Linear Voltage Regulators (2017)
- Power Management for Internet of Things (IoT) System on a Chip (SoC) Development (2017)
- Tradeoffs of LDO Voltage Regulator Architectures and the Advantages of “Capless” LDOs 2019
If you wish to download a copy of this white paper, click here
|
Related Articles
New Articles
- Beyond Limits: Unleashing the 10.7 Gbps LPDDR5X Subsystem
- How to Design Secure SoCs: Essential Security Features for Digital Designers
- System level on-chip monitoring and analytics with Tessent Embedded Analytics
- What tamper detection IP brings to SoC designs
- RISC-V in 2025: Progress, Challenges,and What's Next for Automotive & OpenHardware
Most Popular
- System Verilog Assertions Simplified
- Beyond Limits: Unleashing the 10.7 Gbps LPDDR5X Subsystem
- System Verilog Macro: A Powerful Feature for Design Verification Projects
- Design Rule Checks (DRC) - A Practical View for 28nm Technology
- How to Design Secure SoCs: Essential Security Features for Digital Designers
![]() |
E-mail This Article | ![]() |
![]() |
Printer-Friendly Page |